 |
"Tecnologia Meccanica" moved into the wider "Tecnologia",
since the word meccanica (mechanical) is surpassed by the
present company global activity. Despite our small
local dimensions
we found us competing in many different technological sectors
reserved to the big technological players.
With the Micronization
Technology spin-off, many technologies have been
studied & incorporated in the company know how, these
technologies are offered in
Open Source as technology transfer to everyone,
because we believe that the Future as well the Present is in
the complete and free information sharing.
read more |
|
 |
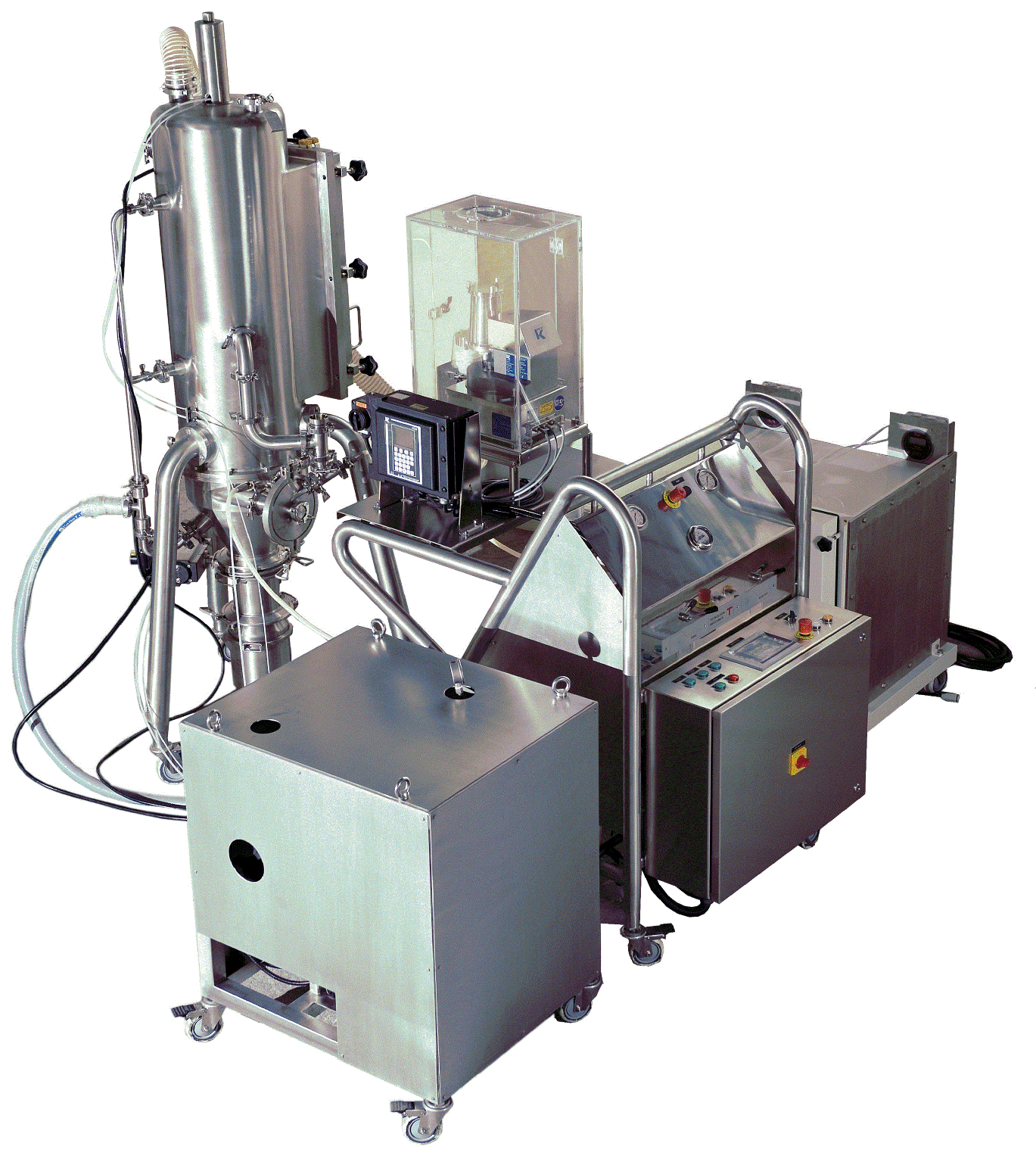 |
Fluid Jet Mill plant with pgcs, modular execution.
The Process Gas Conditioning is a System designed for
introducing metered moisture or organic solvent into the
process gas stream to suit the products requirements.
It is particularly indicated if the source is dry
nitrogen, more than the 90% of the process gas can be
conditioned.
read more |
|
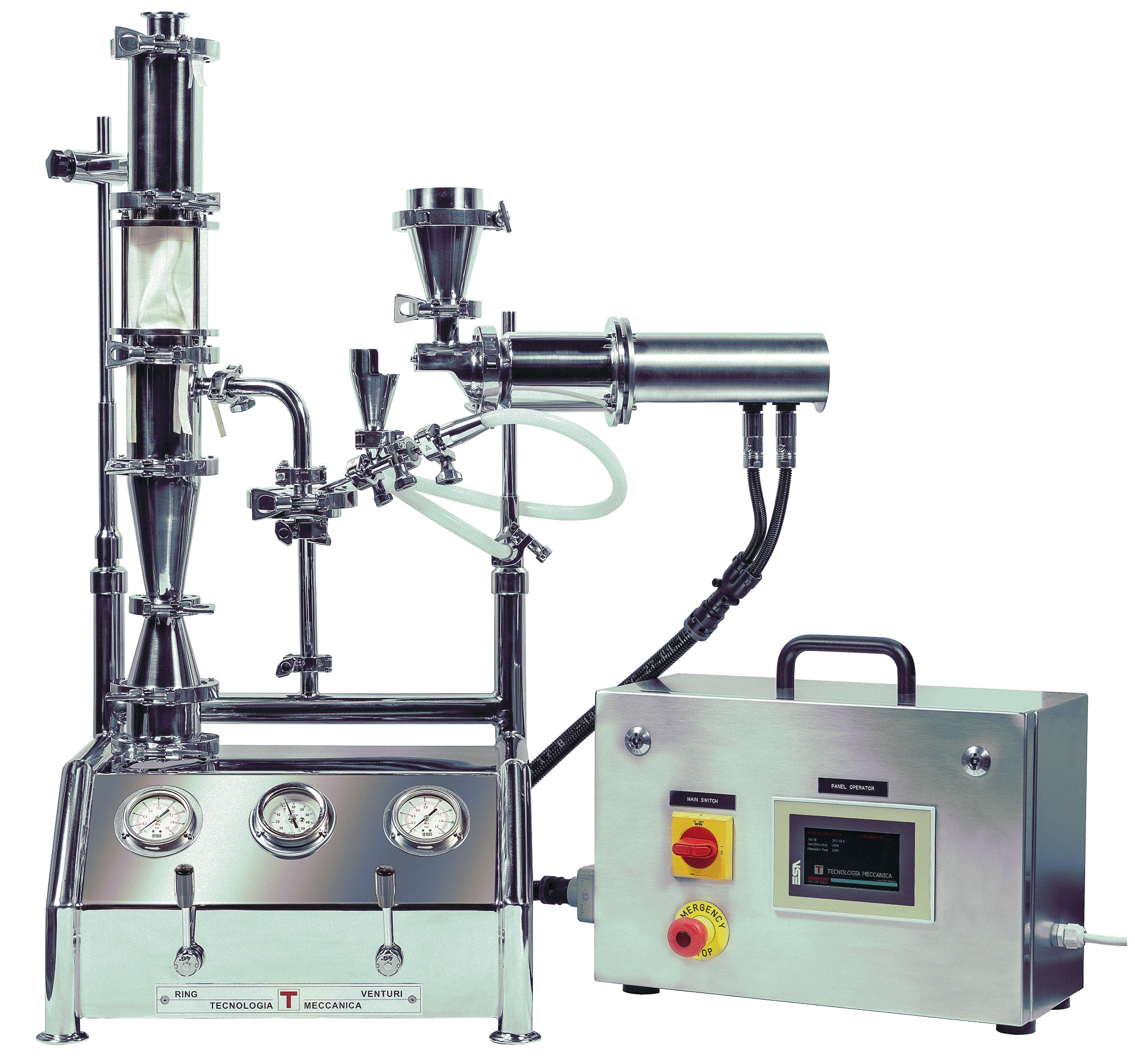 |
Laboratory line for R&D, unlimited configurations.
These fluid jet micronizers share the 70% of the
components and can dock 4 different milling chambers.
Micro twin screw feeder as well compact micro devices are
available in order to process API, HPAIs or NCE.
read more |
|
|
|
 |
 |
MOSCAB's manufacturing and the endorsment to the project
B.I.G. Bubble International Geyser. |
|
 |
Micronization with conditioned process gas, design for
introducing metered moisture into the process gas stream. |
|
 |
Spare parts printed locally with 3D printing technology
at customer premises.
read more |
|
|
 |
 |
Design for the coral reefs restoration, based on net
frames & opportunity corals.
read more |
|
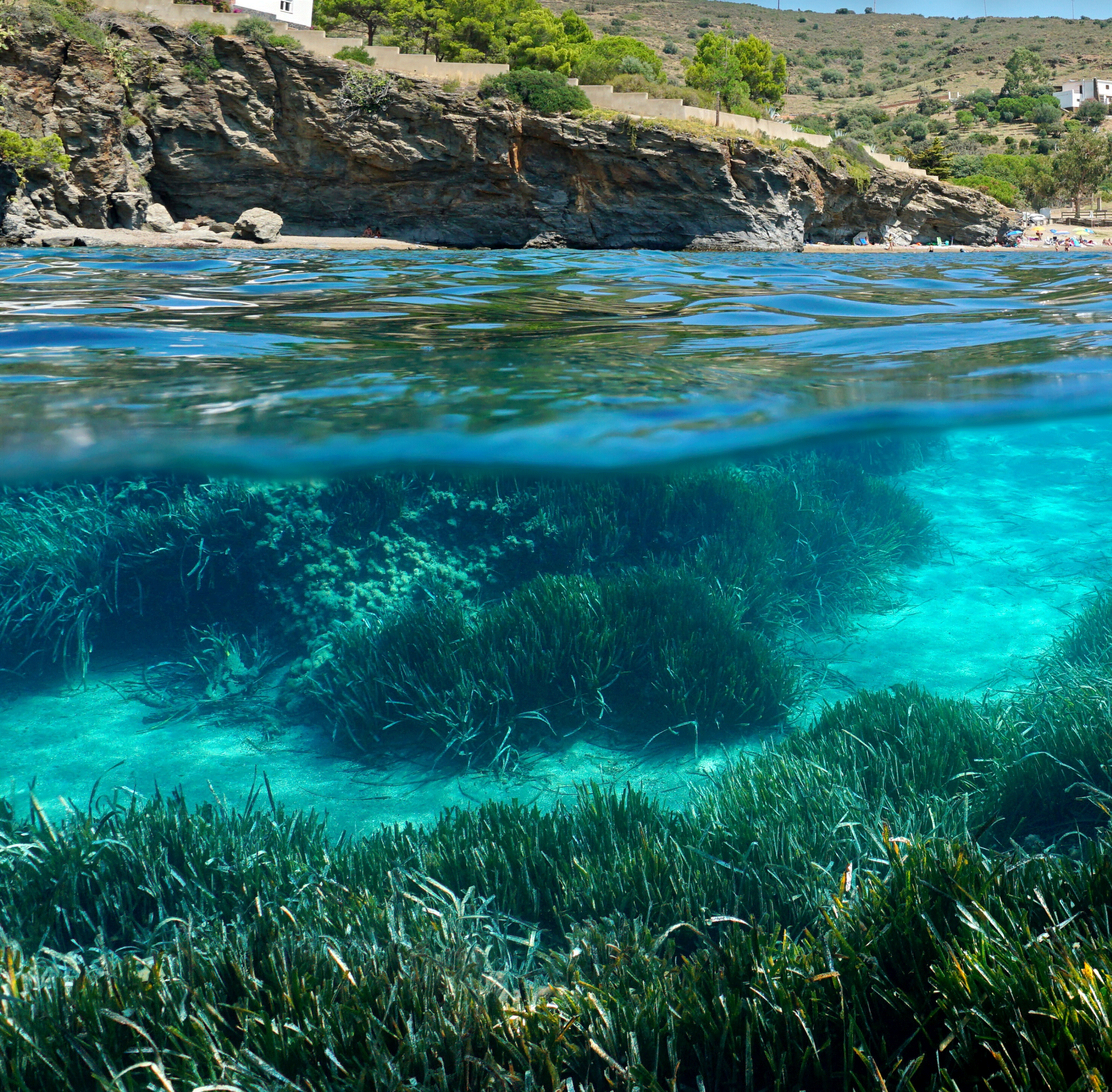 |
Experimental technology for Posidonia Oceanica planting.
read more |
|
|